Explosion Protection
Explosions are suddenly, with enormous speed, occurring oxide reactions that generate a temperature and pressure increasement. Most well-known are reactions of flammable gases, vapours, or dust together with oxygen out of the air.
The Basis for an Explosion
As a rule, three factors must be present simultaneously for explosions to happen in atmospheric air.
Flammable material (in ignitable quantities)
Oxygen (in the air)
Ignition Source
Hazardous areas can develop in production and workplaces wherever the first two preconditions for an explosion are fulfilled. Typical hazardous areas form in chemical factories, refineries, enameling plants, paint workshops, cleaning equipment, mills and stores for milled products and other combustible dust, in-tank facilities, and loading areas for flammable gases, liquids, and solids.
The first two preconditions – the flammable material and air – must be present in justified quantities between LFL and UFL (Lower Flammable Limit and Upper Flammable Limit) to form an explosive atmosphere. The statutory definitions of explosion protection – derived from the health and safety at work regulations – are about workplaces. For this reason, explosion protection is generally limited to describing reactions with oxygen in the air.
Oxidation reactions commonly involve increases in heat and pressure and therefore fulfill the criteria of an explosion.
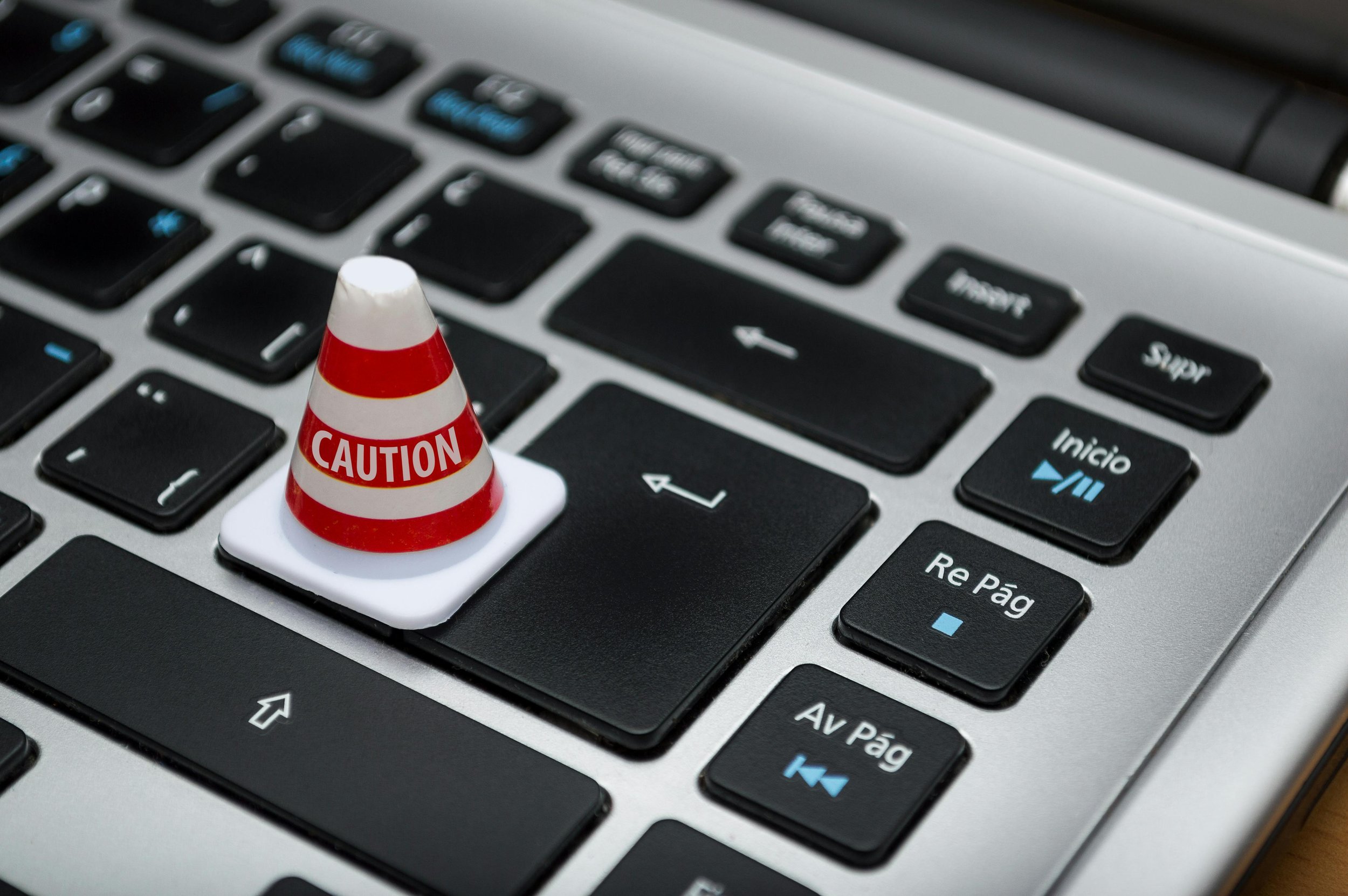
Measures of Explosion Protection
Primary Explosion Protection
Primary Explosion Protection aims at either sub-situating or reducing the quantity of the flammable substances or the atmospheric oxygen to a level where there is no danger of an explosive mixture forming.
Increased air supply air flushing through ventilation can be achieved by structural measures; for example, the open layout of filling stations where the potentially explosive atmosphere is minimal. Replacing atmospheric oxygen is not an option for areas where people work. For this reason, the measures available for such locations are limited to:
Avoidance or restriction of flammable substances which are capable of forming an explosive atmosphere.
Avoidance or restriction of the release of the flammable substances and, therefore, formation of explosive mixtures inside and around fittings/valves
For Example, by:
Limiting their concentration.
Using enclosures filled with an inert substance.
Natural or artificial ventilation.
Concentration monitoring using a gas detection system will give an alarm and switch off the system.
2. Secondary Explosion Protection
Suppose, despite primary Explosion Protection measures, a hazardous, potentially explosive atmosphere can form (to the degree that requires measures to protect employees against explosion hazards). In that case, the ignition of this hazardous, potentially explosive atmosphere must be effectively prevented. Therefore, all possible ignition sources are evaluated, and the appropriate protective measures are applied.
Effective ignition sources on equipment and installations can, for example, be prevented using types of protection corresponding to the necessary level of protection. The classification of potentially explosive areas into zones (The frequency and duration of a hazardous explosive atmosphere and the local environmental conditions) forms the basis for defining the level of protection for equipment. Furthermore, it is necessary to know the critical explosion-related figures for the flammable materials (grouping, temperature classes, dust ignition, and smoldering temperatures) and the local ambient conditions.
The explosion characteristics help the owner/ managing operator specify the risk in the area precisely and allow the operating equipment manufacture to select a suitable solution for the operational equipment. Finally, they help the installation engineer select and assign suitable Ex Equipment. Ultimately, this data is found in the Ex Equipment labeling.
3. Tertiary Explosion Protection
If the primary and secondary explosion protection measures are insufficient, additional protective measures shall be taken. The purpose of these is to limit the impact of an explosion and reduce it to occupational health and environmental safety level.
The most common measures to limit the hazardous effects of the explosion are as follows:
Explosion-resistant design: containers, apparatus, and pipelines are built to be pressure shock resistant to withstand an explosion inside.
Explosion relief: bursting discs or explosion flaps are deployed, which open in a safe direction if an explosion occurs and ensure that the plant is not subjected to strain over and above its explosion resistance.
Explosion suppression and preventing propagation of the explosion: Explosion suppression systems prevent the attainment of the maximum explosion pressure by rapidly injecting extinguishing agents into containers and plants. Explosion decoupling restricts possible explosions to individual parts of the plant
Prevention of Explosions
Explosion-proof equipment can exclude one of the preconditions for an explosion – the ignition source- essential to explosion protection. Architectural measures ensure that an explosive atmosphere cannot be formed in domestic areas. However, the conscious restriction of these measures, for example, the intended, unimpeded flow of flammable gases or a reduction in ventilation, can lead to explosions if an ignition source is also present.
The most straightforward way to understand small and safe explosions is by looking at a gaslighter. When the nozzle of the lighter is opened, it releases a small amount of flammable gas. This gas mixes with the surrounding air, the spark from the flint ignites the mixture, and a weak sound has heard the burning. Some distance away from the nozzle, the proportion of the flammable gas is already so low that the explosion and the flame are restricted to the immediate vicinity of the nozzle. In other words, the design of the gaslighter has ensured that it is safe to use.
The effect of an explosion in enclosed spaces and under non-atmospheric conditions – for example, under increased pressure is often more powerful. Just think of the practical application of explosions in vehicle engines.
To attain effective explosion protection against non-controlled, unintended explosions linked to disastrous consequences, it is necessary to remove one of the three factors.
Preventing Spark
In industries where Gases, Fuels, and Vapors are emitted during manufacturing, processing, transporting, and storage. These inflammable fluids include alcohol, acetylene, propane, hydrogen, and gasoline. In addition, dust, such as wood, sugar, and aluminum, are also potentially combustible substances.
When mixed with oxygen in the atmosphere, these combustibles can form an explosive mixture. Likewise, an explosion may occur if an electric spark externally ignites it.
Why Choose Us?
Our global network of specialist environment, health, and safety (EHS) operatives provides extensive, impartial detection services covering all potentially hazardous situations, promoting discussion, and proposing practical and implementable solutions. In addition, our multidisciplinary technical safety and risk management team provides fully integrated support, assistance, and solutions that enable you to manage the risk associated with major accidental events appropriately and systematically.
Working with the Lorcan & Fyon will help you comply with your obligations to protect your stakeholders, the environment, and your business reputation.